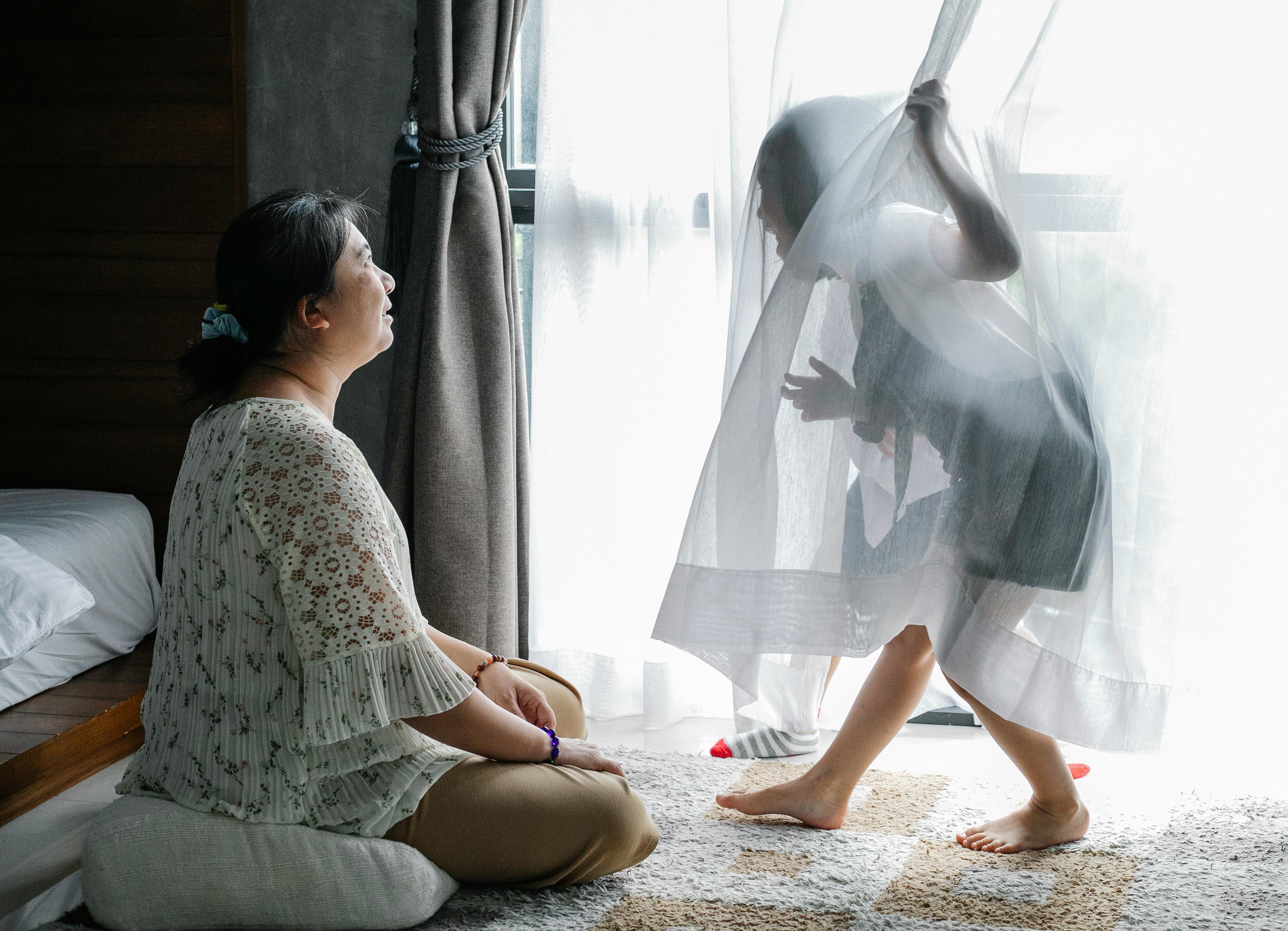
How lean "Gurus" Teach Lean (or Lean Learning by Magic)
Have you ever learned anything from a teacher who waved his wand or sprinkled some (English, math, reading …) pixie dust on you? Well guess what? This is precisely how Lean gurus have traditionally tried to educate average base employees!
Whether you’re starting your Lean journey to establish a Lean culture within your company, or struggling to maintain Lean, you’ve probably heard that it can be nearly impossible to do so. Why is this the dominant thought in the Lean world? I think the answer stems from how Lean has traditionally been taught (or not taught) to classify and file employees; you know, people who are asked to implement Lean principles and tools in their daily work routines! (Author’s note: Call me a cynic, but I’m not convinced that companies claiming to be Lean have taught Lean the basics.)
So how are grassroots taught to embrace Lean as part of their personal culture? Enter “Lean Learning by Magic”. But before explaining what we mean by this, let’s see how those traditionally called to teach Lean – the “Lean Gurus” company – qualified as Lean “teachers.” The model looks like this:
• A few company Lean specialists or key leaders are sent to distant, expensive and time-consuming Lean seminars or enroll in expensive week-long or month-long Lean courses, held online or locally and expect them to become Lean experts overnight.
• After achieving yellow, green, brown, black, magenta, purple, bronze, silver, or gold “certification”, management asks them to quickly implement numerous improvement initiatives (Kaizens) as quickly as possible using a select few: Lean Clueless: team members called to eliminate waste in processes and improve productivity by X%. This is done to get the ROI, company-wide, guaranteed by the gurus of the seminars and training courses, and to impress the CEO, who has no idea about Lean but is eager to make it “work” right now and you’re ready to get the most out of it. Plug it in if it doesn’t!
• If after certifying the company’s Lean Guru, and after holding some Lean flavor enhancement events of the month, Management declares that several of the company’s key leaders should also become Lean Gurus, well then, the company is on its way to Lean careers. , unfortunately, leaving behind the most important resource of the company: its base employees.
• When they’re finally too busy with Lean Gurus, all trying to start Lean Kaizens from the top down in their department, management decides it’s time to educate some lucky rank and file employees in the department (choose any) in Lean.
• The most qualified Lean guru is asked to teach one hour classes on 5-S, Lean or any department problem that needs to be solved and is expected to magically transform an entire department into Lean practitioners … enter, Lean Learning by Magic , which is, in my opinion, NOT learning at all!
I define Lean Learning By Magic as the informal granting of Lean knowledge from someone with higher Lean knowledge to someone with lower knowledge, who is expected to learn “magically” through an effortless (short) exposition (ie, study, review, test … God forbid! – and practical implementation).
At the risk of being frivolous, Lean Learning by Magic allows a Lean Guru to adorn their presence between the base and (figuratively) wave their magic wand, sprinkling Lean Pixie Dust over their subjects for an hour or more. two, waiting for them to suck up the pixie dust (hug Lean?) … magically. Lean Learning by Magic does not require a syllabus, no training manuals, no schedules or routines, no exams, no certification, and it does not actually produce any learning.
If culture is defined as a knowledge system shared by a relatively large group of people (Oh, say, ALL your employees), that is, the sum total of learned behavior, it follows that to maintain this knowledge and behavior you must be continually fed (taught!) or the culture will cease to exist. From time to time, magically sprinkling Lean pixie dust over some employees, removed from the value stream, as time (demand) permits, can never produce a Lean-educated workforce, and can actually prevent a company create a Lean Cultural Transformation.
If employees, across the company, are being asked to become Lean practitioners who seek and know how to passionately and routinely identify and eliminate waste and seek ways to continually improve work processes, then they must be taught formally how to do it. To do this, management must create and maintain a much larger Lean learning environment than the occasional one- or two-hour classes taught by the company’s Lean guru waving his magic wand. Also, just because a Lean Guru understands Lean, it does not qualify him to TEACH Lean, especially if he has; does not have teaching skills (has no idea how to teach), does not have a curriculum to teach, does not have a training manual to teach or provide to students, does not have a regularly scheduled time or place to teach, no assesses comprehension and retention, has no provision for actual or simulated practical implementation of the principles taught, and generally simply does not have a structured or balanced instructional program from which your students can truly learn and feel good about the experience of learning because it has value to them, that is, it can make them more valuable to the company.
Review the following scenarios and ask yourself which scenario would contribute the most to helping a 350-employee company establish, maintain, and continually improve a Lean culture:
• Company “A” has 15 different departments, two veteran Six Sigma black belts, six new Six Sigma green belts, a Lean coordinator, and a 5-S coordinator. Excluding the aforementioned personnel and the remainder of its management force, the company has approximately 300 core employees whose only exposure to Lean training has occurred during preliminary briefings prior to the start of a narrow or highly focused Kaizen improvement event. infrequent, one-to-two hours of on-site Lean training seminars. Although at some point they have been exposed to 5-S and 8-Wastes, management has never asked base employees to name and define each 5-S and 8-Wastes, or to prove in any way that they understand the philosophy. behind and the importance of implementing these two basic Lean building blocks in your daily work routine (culture).
• Company “B” has the same number of Lean practitioners mentioned in the first paragraph above. They have also established a company-wide Lean training program with the goal of helping the entire workforce embrace Lean as part of their personal culture. In addition, employees have been told that there is both a long-term and short-term benefit to the company and to them if they practice Lean in everything they do, especially in the routine search, identification and elimination of waste in processes and department and individual procedures, and in sustaining the company’s active 5-S program. Because the company’s Lean training program requires daily exposure to Lean concepts and principles through daily short lesson presentations (5 minutes) in the shop or office, employees have quickly realized that daily Lean training is just another part of your daily routine. job responsibilities and standards and, consequently, strive to meet the standards, that is, the standards of the company’s Lean culture: “The sum total of your learned behavior.” Use a formal training curriculum, provide training manuals for both leadership and employees, company-wide, present daily, short and formal lessons and discussions, take comprehension and retention tests (weekly quizzes and quarterly exams) , reviewing assessment results, and running hands-on simulations or actual implementations of Lean concepts and principles that are studied weekly, the company has truly created an environment in which Lean can and does thrive, both top-down and bottom-up. above.
Hopefully, you chose Company “B” as the company most likely to help its workforce embrace Lean as part of their personal culture. Obviously, I believe that the key to creating and maintaining the Lean culture is to create an environment that daily and continuously, whatever happens, exposes a company’s workforce to Lean concepts and principles and does so in a structured learning environment. .
Question: What would you rather have? A company of 200 employees with a few highly qualified and certified Lean gurus who uniquely implement Lean initiatives. Or a company whose entire workforce has been educated in Lean to seek out, identify and eliminate waste and continually, routinely, day after day, look for ways to improve individual and department processes, because (having been taught), it really understand the value this has for the company and for themselves. This kind of cultural transformation cannot be achieved with Lean Learning by Magic! Having Lean gurus try to “teach” Lean without a formal training program in a structured setting (similar to the one they studied Lean) is like asking them to teach Lean by waving their magic wand … it just doesn’t work that way!
John ramuno
No Comment